Browsing the World of Fasteners and Machining: Approaches for Precision and Rate
In the intricate world of fasteners and machining, the quest for precision and rate is a continuous difficulty that requires meticulous interest to information and tactical preparation. From comprehending the diverse range of bolt types to choosing optimum products that can endure strenuous needs, each action in the process plays a critical duty in achieving the preferred result. Accuracy machining techniques even more raise the intricacy of this craft, requiring a delicate balance in between technological experience and innovative methods. As we dig right into the strategies that can enhance both speed and performance in this domain name, the interaction in between quality assurance measures and functional excellence becomes an essential centerpiece.
Understanding Fastener Types
When choosing fasteners for a project, recognizing the numerous kinds offered is critical for making certain ideal efficiency and dependability. Fasteners can be found in a vast array of kinds, each developed for specific applications and demands. Bolts are used with nuts to hold products together, while screws are versatile bolts that can be made use of with or without a nut, depending on the application. Nuts, on the other hand, are inside threaded fasteners that mate with screws or screws, offering a secure hold. Washing machines are necessary for dispersing the tons of the fastener and protecting against damages to the material being attached. Furthermore, rivets are permanent bolts that are excellent for applications where disassembly is not called for. Comprehending the distinctions between these bolt types is essential for selecting the right one for the job, making certain that the link is strong, durable, and trustworthy. By selecting the ideal fastener kind, you can optimize the performance and durability of your job - Fasteners and Machining.
Picking the Right Products
Understanding the value of picking the right materials is vital in ensuring the ideal performance and integrity of the selected fastener kinds discussed previously. When it pertains to bolts and machining applications, the material choice plays a critical role in figuring out the general toughness, resilience, corrosion resistance, and compatibility with the desired atmosphere. Various products use differing buildings that can substantially influence the efficiency of the bolts.
Usual materials made use of for fasteners consist of steel, stainless steel, aluminum, titanium, and brass, each having its unique toughness and weak points. Steel is renowned for its high stamina and longevity, making it appropriate for a vast variety of applications. Selecting the ideal product involves thinking about factors such as stamina requirements, environmental problems, and budget restrictions to make certain the preferred efficiency and longevity of the fasteners.
Accuracy Machining Techniques
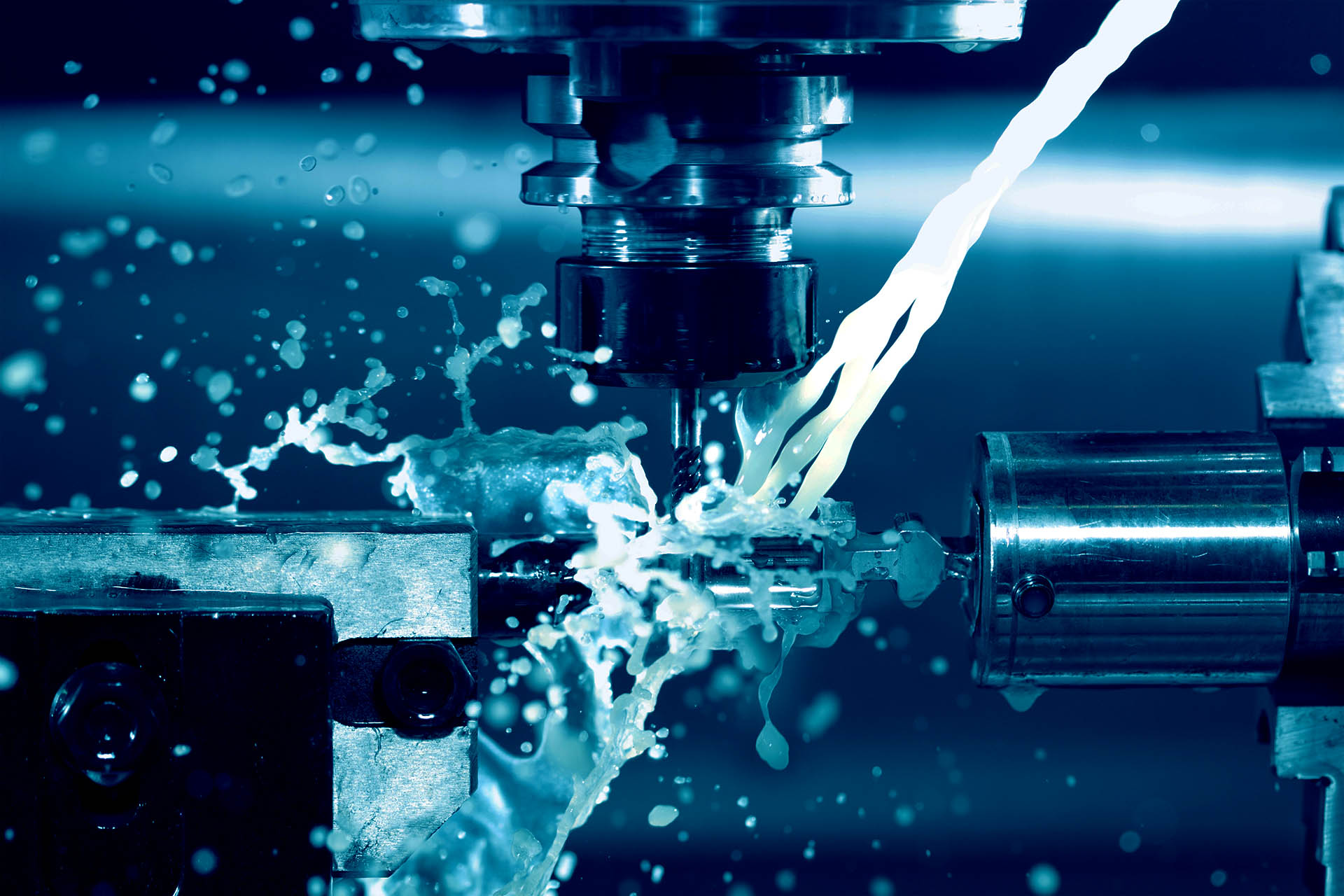
Along with CNC machining, click for source other precision strategies like grinding, turning, milling, and exploration play important duties in fastener production. Grinding assists achieve great surface area finishes and limited dimensional resistances, while turning is commonly utilized to create cylindrical parts with precise diameters. Milling and exploration operations are vital for forming and creating openings in fasteners, guaranteeing they fulfill exact specs and feature appropriately.
Enhancing Speed and Effectiveness
To optimize bolt production procedures, it is crucial to enhance operations and carry out efficient approaches that complement accuracy machining techniques. Automated systems can take care of repeated jobs with precision and rate, allowing employees to concentrate on more complex and value-added tasks. By combining these methods, manufacturers can accomplish an equilibrium between rate and precision, eventually boosting their affordable side in the fastener sector.
Quality Control Procedures
Implementing strenuous top quality control procedures is essential in guaranteeing the reliability and uniformity of bolt products in the production procedure. Fasteners and Machining. Quality control steps encompass numerous stages, beginning from the choice of raw materials to the final inspection of the ended up bolts. This involves analyzing aspects such as material composition, durability, and strength to ensure that the bolts satisfy sector requirements.
Routine calibration of devices and equipment is necessary to maintain uniformity in manufacturing and guarantee that bolts meet the required tolerances. Implementing stringent methods for determining and addressing problems or non-conformities is vital in stopping substandard items from entering the go now marketplace. By developing a comprehensive quality assurance structure, manufacturers can support the online reputation of their brand and deliver fasteners that satisfy the highest standards of performance and toughness.
Conclusion
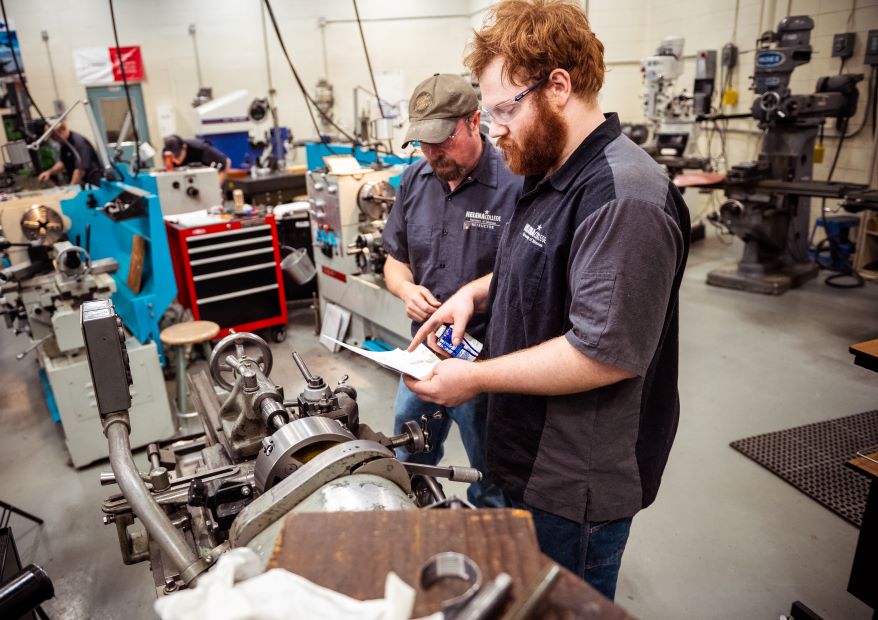
In the detailed world of bolts and machining, the pursuit for accuracy and rate is a continuous challenge that demands meticulous attention to detail and tactical planning. When it comes to fasteners and machining applications, the material option plays a vital duty in establishing the total toughness, longevity, deterioration resistance, and compatibility with the desired setting. Accuracy machining includes various advanced methods that guarantee the tight resistances and specifications needed for bolts.In addition to CNC machining, other accuracy strategies like grinding, turning, milling, and drilling play vital duties in bolt production.To optimize bolt production procedures, it is crucial to simplify procedures and execute efficient strategies that enhance precision machining techniques.
Comments on “Fasteners and Machining: Integrating Accuracy and Toughness in Manufacturing”